ABOUT CATHODIC PROTECTION |
 |
 |
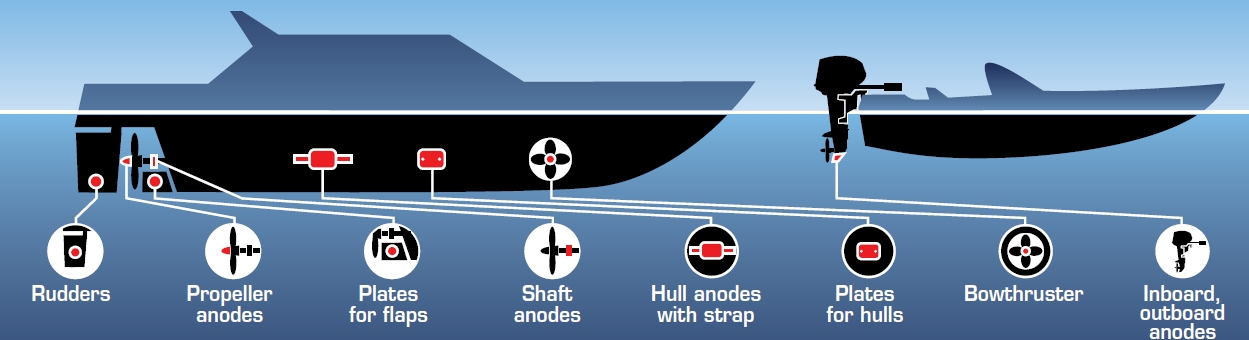
The most effective method to control undesirable effects of metal corrosion is Cathodic protection. This technique, used worldwide since the 1930’s was originally introduced in the early nineteenth century to meet the needs of the British Navy and also used, with excellent results, for the protection of underground structures.
When it comes to Cathodic protection, especially in the leisure craft, industry we usually think of sacrificial anodes. In fact the method is essentially divided into two clearly defined technical areas: passive Cathodic protection (sacrificial anodes) and active Cathodic protection (impressed current). Both techniques offer protection of metallic structures that are subject to wet corrosion. This is achieved by lowering the natural electrochemical potential of the metal to be protected by inducing a flow of current between the anode and the cathode (structure). There are many fields of application of Cathodic protection: marine (nautical, commercial, offshore, inshore, industrial, etc.) to land applications (aqueducts, pipelines, oil pipelines, etc.) as well as those applications where you need a specific defence against electrochemical corrosion.
Sacrificial anodes, more commonly known as “zincs”, are installed at specific locations on the underwater section of a hull as part of a passive cathodic protection system. The objective is to protect any metal structures immersed in water, from corrosion.
The principle of operation is very simple: the anode is made of an alloy which has an electrochemical potential less than most metals used on a boat, which enables an electrochemical process to take place. A current will flow from the anode to the cathode (the metal structure to be protected) to equalise the potential difference, resulting in the loss of electrons by the anode and its accelerated dissolution in water. Consequently, the metal structure in contact with the anode, has a greater reserve of electrons that are also utilised to power the electrochemical process which otherwise would have contributed to the corrosion of its surface. In this situation the metal is protected from the electrochemical corrosion, depending on the type, quantity of anodes fitted and their relative position. To achieve this type of protection it is essential to create a potential difference which induces a current flow between the anode and cathode. This is only possible by connecting the metal material to be protected, with a metal of lower nobility; as a consequence this will work as a sacrificial anode. Our objective in practise, whenever we install sacrificial anodes on a metal structure, is to bring the electrochemical potential of the metal to be protected to a certain value (the so called protection level) that generally appears to be more negative than the initial one.
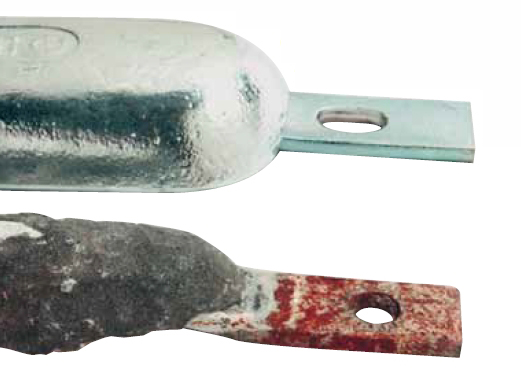
The first property to consider is their electrical potential. All metals generate a negative voltage (as compared to a reference electrode) when immersed in water. The lower – the more negative - the voltage, the more active the metal is considered to be, for example:
Magnesium generates -1.6 Volts, i.e. negative 1.6 volts.
Aluminum sacrificial anode alloy generates -1.1Volts
Zinc, -1.05 Volts
In order to provide protection, the highest practicable voltage difference possible is required between the sacrificial anode and the metal to be protected.
For example, if zinc is used to protect a bronze propeller, a “driving or protecting voltage” of negative –0.75 volts will be available, i.e. zinc at -1.05 volts minus bronze at -0.3 = - 0.75 volts.
If aluminum anodes are used this increases to -0.8 Volts.
Magnesium anodes increase this to -1.3 volts.
The bigger the difference in voltage, the more protection you get. But, beware, some materials (aluminum) can be “overprotected” – more about that later.
The best anodes are made from an "activated alloy" in which catalysts have been added to ensure that the anode gives 100% of itself in the purpose of protecting your boat from corrosive action.
What is Galvanic Corrosion? If you've noticed corrosion on the metal parts of your boat located below the waterline, you are the victim of "galvanic corrosion". The scientific term "galvanic" corrosion describes the type of corrosion that anodes are intended to absorb. This corrosion is normally caused by different metals being near each other in salt water. Galvanic corrosion, an electromechanical action, causes metal parts to decompose. This destructive process is caused by electrolysis, an electric current set up between the metal parts of your boat, with salt water as the electrolyte. The effect is like a flashlight battery -- an electrical current is created and continues until one of the metals is eaten up -- the battery goes "dead".
What is Electrolytic Corrosion? If you see an accelerated corrosion on the metal parts of your boat located below the waterline, you are the victim of "electrolytic corrosion". The scientific term "electrolytic" corrosion describes an accelerated type of corrosion that occurs when an electric current is added to the water surrounding your boat (usually at a dock). This corrosion is typically caused by faulty wiring that permits an electric current to enter the water. This corrosion, combined with galvanic corrosion, is also an electromechanical action which causes metal parts to decompose, but at a very accelerated level. This destructive process is also caused by electrolysis, which is an electric current set up between the metal parts of your boat, with salt water as the electrolyte, but it can be much more damaging in a very short time.
The protection of the underwater metal parts on your boat or motor from corrosive electrolytic action is a very real and necessary concern. The use of an activated alloy such as an “anode” will help. Anodes will distract the corrosion action to itself and away from expensive metal parts. Fortunately anodes are relatively inexpensive and are readily available. Factors such as warm water temperatures, polluted water and stray current corrosion can cause your anodes to waste away at an accelerated rate so it is wise to check them on a regular basis.
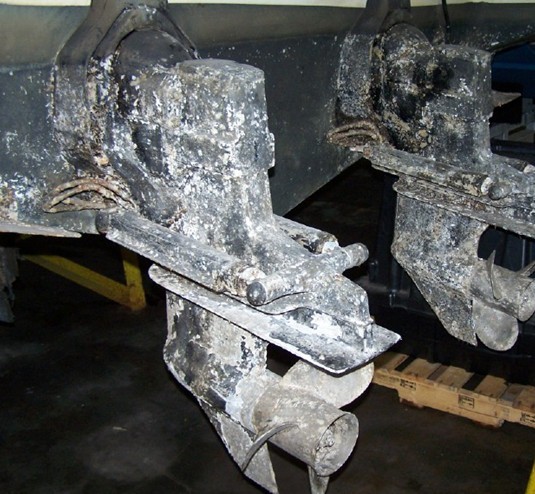
An important thing to remember is that you must complete a "circuit" for the anode to be effective, which means that the zinc must be in direct contact with the metal components of your boat located below the waterline. This is the reason that a hanging grouper-style of anode comes with a wire and metal clip that is intended for attachment to a "ground" within your boat. When attaching a zinc anode to a prop or shaft, please be certain that the point of surface attachment is clean and "bright" so a good contact is made, completing the circuit. Also, never paint over a zinc with bottom paint, which will only isolate and protect the anode from its intended purpose.
Products
ANODE, ALUMINIUM, SUZUKI 20-30 HP
REC55125-91L01AL
ANODE, PROPELLER, FERRETI, SHAFT Ø 55-70 MM
TEN00478
SHAFT ANODE, ZINC, Ø 30 MM
TEN00506
|